THANK YOU FOR SUBSCRIBING
Editor's Pick (1 - 4 of 8)
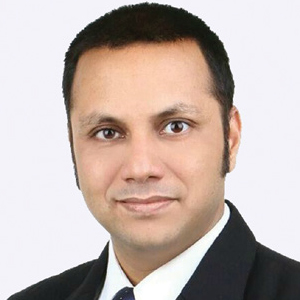
Abhishek S, Chief Digital Officer, RGE
The vibration signals from bearings, for instance, are monitored for their spectrum and enveloping energy levels passes through a clustering algorithm to identify abnormal operation patterns. Based on these patterns, we can then perform prediction of the anomalies by using historical vibration data and also, records of loss reports that contain machine equipment failures. When a known operation indicates a certain pattern, it would warrant for an alert or alarm, directs the right response alternatives to the available knowledge worker to prioritize and execute the corrective action.
However, the interoperability of various industrial systems remains a major obstacle that needs to be addressed by manufacturers. The heterogeneous environment of plant automation systems comprising of scheduling, product recipes, equipment availability, and other elements are necessary for achieving a realistic production plan. International Society of Automation (ISA) is an organization that sets standards in the field of automation developed ANSI/ISA-95,an industry-standard providing a guideline on plant-wide system and implementation model, facilitating ease of communication across the enterprise, lowering the total cost of ownership and enabling error-free system integration.ISA-95 standard uses a top-down approach flow dispatching information from a pre-computed schedule to the plant floor. Traditionally, production targets are defined at enterprise resource planning (ERP) and the feasibility of a schedule is assessed by the manufacturing execution system (MES) if the targets can be produced. The values of the production batches are monitored by PI system, a real-time data acquisition repository integrated with sensor readings and supervisory control and data acquisition (SCADA) system providing visibility of equipment status. Business then uses this information and to look for correlations, perform comparison, and optimization of different lots in production. This information are also used to determine if maintenance is required on the equipment. Therefore, it’s critical to efficiently transfer these disparate data into a more meaningful and actionable manner that are shared between the production environment and business applications for real time use. With the application of advanced algorithms, business are able to control quality and maximize production autonomously, by applying a simplified predictable process that displays the production plan, maintaining its flexibility on accommodating for changes and creates an environment to communicates effectively.
The application of industry 4.0 is vital to any business, to remain competitive and ensure future growth. Industry 4.0 maturity model is an integrated approach to ensure the success of transformation initiatives. A full comprehensive assessment of the company’s current state, visibility over its manufacturing process are needed to gain comparable and tangible insights. To achieve this, the business has introduced the use of operational excellence platform to achieve a competitive superiority between its mills. This is to drive efficiency, reduction in operational cost and being able to run the mill operation in a predictable manner to meet customer demands. These initiatives are then aligned with Kaizen initiatives for continuous improvement across the entire organization. By having transparency of the existing process and methods, competitive advantage is maintained throughout the manner of standardization and optimization of the process formulas across the mills .Real time data collected from multiple systems are visualized in the form of dashboards with event based notifications and escalations workflows provide instantaneous support by roles. Through the use of intelligent analytics and models, historical data are used to baseline, evaluated and predict a future state. Performance data are then benchmarked to help alleviate weaknesses and identify improvement, in accordance with business scorecards and strategies. Market demand and productivity driven by asset conditions information can be integrated into supply chain planning systems, to help and notify production line in the event of a bottleneck, ensuring no loss in production yield and quality. This is where the genuine emphasis on 'disruptive' solutions are developed, bringing operation excellence to every layer of the business.
To push ahead with Industry4.0, a phased step by step approach in achieving excellence maturity Evaluate your digital roadmap with your current state and subsequently break it down to areas of, priorities and focus on the measures that will develop and shape your digital journey, ultimately delivering value for your business.
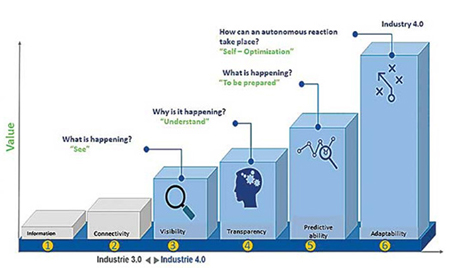
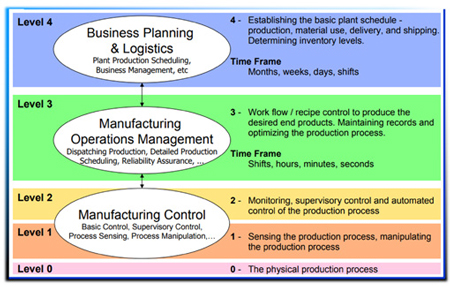